Streamlining Oil and Gas Supply Chains for Agility and Resilience
The oil and gas (O&G) supply chain is among the most complex in the business universe. Materials and resources must flow seamlessly across remote and diverse locations—and in a timely manner—to ensure smooth delivery of critical shipments for uninterrupted operations. However, fragmented systems, manual processes, and communication gaps pose serious challenges, leading to delays and inefficiencies. In the wake of the COVID-19 pandemic that disrupted supply chains worldwide, a leading global oil and gas company took the opportunity to transform its procurement processes to create a more resilient and agile supply chain.
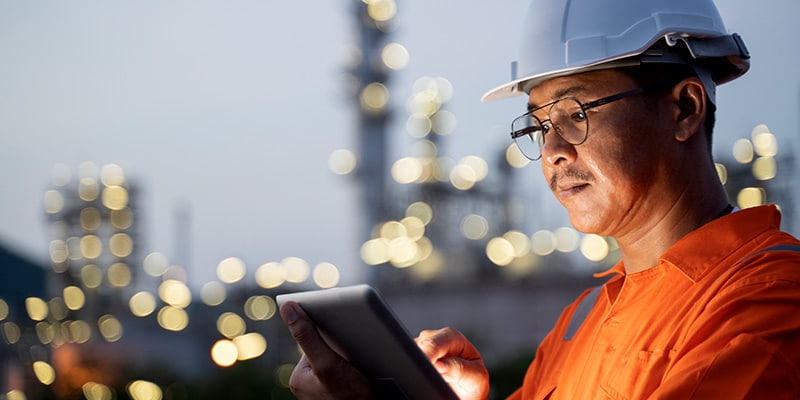
Client Brief
The client, an integrated energy company with operations spanning more than 60 countries, depended on material coordinators (MCs) to manually manage and track the delivery of critical materials. The existing process required MCs to navigate multiple disconnected systems to determine shipment status. This fragmented process had created bottlenecks, impacting operational efficiency and raising costs owing to delays.
Challenges
There were several inefficiencies hampering the company’s supply chain processes. Different parts of the supply chain used disconnected systems, each with its own terminology and structure. This made it difficult to track materials across various locations. The fragmentation prevented real-time visibility, making it challenging for MCs to provide timely updates. Also, most of the manual processes involved considerable time and effort to gather data from disparate systems. Further, the absence of a streamlined channel of communication meant that teams across locations struggled to coordinate among themselves for accurate information. The pandemic intensified these challenges, creating greater uncertainty and sending costs soaring.
Infosys Solution
Infosys worked closely with the client to develop a unified, user-friendly platform that would simplify supply chain operations and enable real-time collaboration. By leveraging their existing SAP Fiori infrastructure, Infosys created a real-time digital view to track material status and shipments. This eliminated the need for multiple system logins and manual data consolidation. The platform was integrated with Microsoft Teams—a tool that the client already used—enabling MCs to collaborate more efficiently. An intuitive help feature was also built into the platform, offering users guidance when needed. Users were also able to share their experience with the developers, helping Infosys make further improvements to the solution. The entire solution was developed and deployed in just 16 weeks.
Business Benefits
With significant improvements across the board, the new platform:
- Reduced shipment delays: Improved visibility, communication, and collaboration helped reduce shipment delays by 28%
- Increased cost savings: Reducing delays and inefficiencies resulted in an estimated US $27 million in savings annually
- Improved user satisfaction: The ease of use and effectiveness of the platform helped receive consistently high user ratings of 4+ stars
- Boosted productivity: Minimizing manual tasks allowed MCs to focus on strategic tasks, boosting overall productivity
- Enhanced scalability and resilience: Leveraging existing SAP infrastructure ensured cost-efficiency and scalability for future needs
Authored by Pradip Pandya, AVP & Client Partner, Infosys.