Insights
- Aircraft maintenance, repair and overhaul (MRO) is expected to recover to pre-pandemic levels by 2024 and grow at a 2.8% CAGR over 2025-2030, to become a $118 billion industry.
- MRO’s key metrics are quality assurance, cost control, and turnaround time, with digital technologies to reach a balance between them.
- However, enterprise applications need to be upgraded to keep up with industry demands.
- MRO technicians need to collaborate with wider engineering teams to resolve issues they cannot address. Early collaboration with accurate information sharing is a way to speed up the process.
- MRO industry is the last mile in the aircraft lifecycle. It plays a key role in sustainability, using advanced technologies for end-of-life management of critical parts.
According to the International Air Transport Association (IATA), the number of air travelers will double this year from 2020 levels.1 But aircraft and their engines that have been grounded for months need services and certification to become airworthy. The maintenance, repair, and overhaul (MRO) industry should be ready for this recovery.
A pre-pandemic study forecasted the global MRO industry to grow at a compounded annual growth rate of 4.3% over 2018-2025, to become worth $110 billion by 2025.2 According to a more recent study, MRO demand will recover to pre-pandemic levels by 2024. However, the demand will grow at a 2.8% CAGR over 2025-2030 to reach $118 billion by 2030, 13% below the pre COVID forecast of $135 billion.3
The air travel bounce-back, carbon emission reduction for sustainability, and employee recruitment and retention will stress the MRO industry
Going ahead, the fleet mix will also change due to the inclusion of fuel-efficient, narrow-body aircraft and the retirement of older aircraft. Along with this change in MRO procedures and tools, the demand bounce-back, carbon emission reduction, and hiring and retention of employees will stress the MRO industry.
MRO’s key metrics have always been quality assurance, cost control, and turnaround time. Quality assurance is critical due to the requirement of high safety standards in the aviation industry. MRO players face a challenge balancing the standards with the need to reduce costs and boost the speed of operations.
While technology helps achieve the balance, enterprise applications need to be upgraded to keep up with industry demands. For example, automation of workflows and migration to a cloud-based setup can enhance reliability and resilience. Also, better integration between applications can accelerate information flow, reduce human errors, and support rational decision-making.
MRO players are increasingly utilizing advanced technologies to effectively address cost, time, and quality aspects (Figure 1). For instance, Rolls-Royce recently launched virtual reality-based immersive training for its customers. GKN Aerospace uses laser deposition for its additive layer manufacturing initiative to make on-demand parts. Test-Fuchs, an aviation testing systems manufacturer, uses digital twins for its equipment.
Digitization helps achieve the balance between cost, quality and cycle time. But applications should be upgraded to keep up with industry demand
Figure 1. Technologies to manage cost, time, and quality needs of the MRO industry
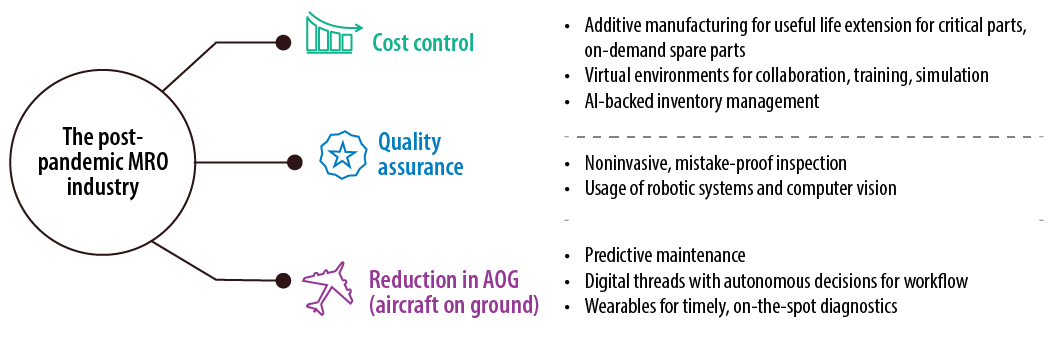
Source: Infosys Knowledge Institute
Induction planning in a connected shop
The shop-based MRO cycle starts with induction planning when an aircraft or an engine arrives for repair (see Figure 2). This phase involves evaluation and quality checks based on the aircraft’s flight history, to determine the next actions. Job cards are prepared, and inventory checks are carried out. In this phase, the lack of integration between equipment, inventory levels, and technicians is a challenge.
Figure 2. A representative MRO shop workflow
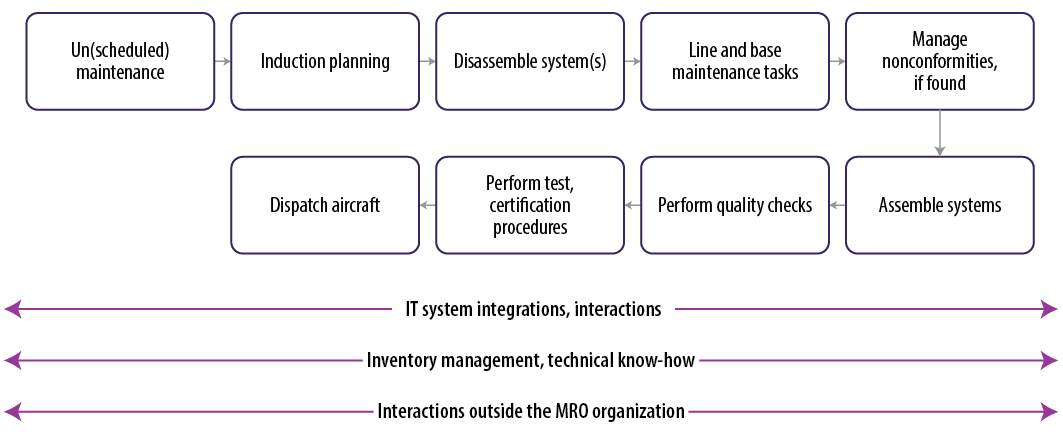
Source: Infosys
Airbus implemented Skywise, its cloud-based aviation data platform. It is one reference of information with multiple sources of input, for operational efficiency and planned MRO for preventive maintenance. To address the integration challenge in an MRO shop, a “connected factory” uses Internet of Things (IoT) to provide visibility to machine conditions and thereby avoid downtime.
Infosys implemented a connected factory for an aerospace manufacturer and its MRO facilities, resulting in end-to-end visibility across its shops.4 Sensors were installed to monitor machine conditions across more than 500 machines in 11 facilities. A wireless shop floor network integrated the sensor data feed with analytics and data visualization tools to aid decision-making. As a result, on-time deliveries improved by 5%, productivity by 15%, and overall equipment effectiveness by 20%.
Disassembly through assembly of systems
In the overall MRO process, disassembly, line and base maintenance, and final assembly take substantial time and pose some of the biggest challenges. The key objective is to carry out the recommended operations while ensuring adherence to airworthiness requirements and certification. The majority of the work is done through approved manuals from original equipment manufacturers (OEMs) alongside specific MRO guidelines and work instructions. The challenges in these phases are the time taken to resolve an issue, managing nonconformities, collaboration with external experts when required, and siloed IT systems that are not well integrated with each other. These steps involve high reliance on the experience and skills of technicians.
Managing nonconformities
MRO technicians often need to collaborate with wider engineering teams to resolve issues they themselves could not address. The way to speed up traditionally slow processes is to ensure early collaboration sharing complete and accurate information from the start. Experts can look at the issue in real time through remote diagnostic capabilities involving video and data sharing. They can assess the issue and provide necessary instructions. Safran has deployed a remote visual support solution to enable real-time collaboration between its MRO technicians and remote experts.
MRO shops address diverse defects, ranging from wear and tear to full-blown cracks. The overall turnaround time is defined by the identification and measurement of the defect, its classification, and containment. Computer vision with image analytics can perform these tasks without human intervention. This, combined with enterprise IT, can pull up similar prior instances to provide an accurate solution to manage the defect. For instance, Ford uses computer vision with artificial intelligence to spot wrinkles in its car seats, avoiding manual inspection.
However, training machines using past images and providing correct interpretation require huge sets of images of various types of defects. Boeing faced this challenge for its “industrial metaverse” experiment, focused on futuristic aircraft maintenance. It wanted to use augmented reality to compare a plane’s present condition with its past by using historic data. But the challenge was in the creation of training data sets. Boeing eventually used a digital twin to create computer-generated, curated images.5
MRO technicians need to collaborate with wider engineering teams to resolve issues they cannot address.
Many MRO players still follow paper-based workflows and punch in the information later. Wearables integrated with IT systems make it possible to execute operations with voice-based commands. Delta Airlines, for example, uses a robotic exoskeleton as a wearable to sense the situation and augment the physical strength of its maintenance staff. Honeywell’s Vocollect application allows a technician to perform various operations and execute the workflow through headset-enabled voice commands. Connectivity of IT systems with wearables, cyber security, and the training of technicians are some of the challenges to overcome in adopting this technology.
Quality checks before delivery
Inspection for quality assurance is an important phase to ensure that any change made to a system meets the necessary checks before its delivery. Computer vision is useful to compare the image of a restored part with that of an ideal part to ensure quality.6 Many MROs use drones to analyze aircraft and find defects that are difficult for a human to spot. When combined with computer vision, drones can help in quality inspection after restoring the external aircraft surface — after painting, for example.
Many operations cut across the complete life cycle of an MRO job. These are critical use cases applicable at each of the above stages in the workflow, and technologies can help each of these operations.
Remote application access
During the initial pandemic-led lockdowns, remote access of on-premises documents and applications became a major challenge. Such applications are a risk of single point of failures when they are not accessible. European airline Volotea faced similar challenges in its MRO operations.7 Its MRO software faced challenges due to end user access, security, and flexibility during seasonal workloads and changes to aircraft fleet. The airline migrated its MRO application to a cloud-based setup with open-source software. This setup offered elasticity, security with single sign-on for authentication, and cost reduction.
A hybrid IT infrastructure setup with a mix of on-premises applications where necessary, integrated with public and private cloud setups as a backup, is an ideal situation.
Simulating complex situations
The what-if scenario approach simulates complex situations before they occur and helps MRO firms prepare for such situations. Also, digital twins help assess the impact of critical decisions virtually before their physical implementation. However, digital twins require the sharing of the intellectual property of aircraft systems between OEMs, MRO players, and airlines, which is a challenge.
MRO player Lufthansa Technik did not face this issue because it also manufactures engine components. In 2017, Lufthansa Technik launched AVIATAR, its digital twin platform, to create a replica of its fleet of aircraft for condition monitoring, predictive maintenance, and fault analytics.8 The company used digital twins for the initial design phase of aircraft cabins and for logistics to establish a digital warehouse.
On-demand additive manufacturing
Parts replacement is one of the biggest cost items in aircraft maintenance. Components amount to 24% of the direct maintenance cost of airlines.9 Parts are replaced either due to their low life remaining or because they cannot be repaired in exact form, fit, and function to guarantee pre-repair level of functionality and safety. Additive layer manufacturing (ALM) has proven to be useful in restoring parts to their original form, fit, and function. ALM enables on-demand parts manufacturing, avoiding the need to keep inventory in stock. However, it supports only a narrow range of high-cost materials, acting as a dampener for ALM adoption.
The advancements in MRO operations will only succeed with proper training and physical and technical assistance.
Immersive training environments
Finding and training the right talent to operate complicated aircraft systems is a challenge in the MRO industry. Advanced technologies can help in remote training. For instance, Rolls-Royce was finding it difficult to ship physical engines to its airline clients for training purposes. To resolve this, it launched a virtual reality-based learning course to provide an overview of the design, construction, operation, and repair of aircraft engines.10 The virtual course saves training cost and offers flexibility of timing and access to complex systems not reachable in a real engine.
Figure 3. Foundational and advanced technologies to meet the key business metric targets
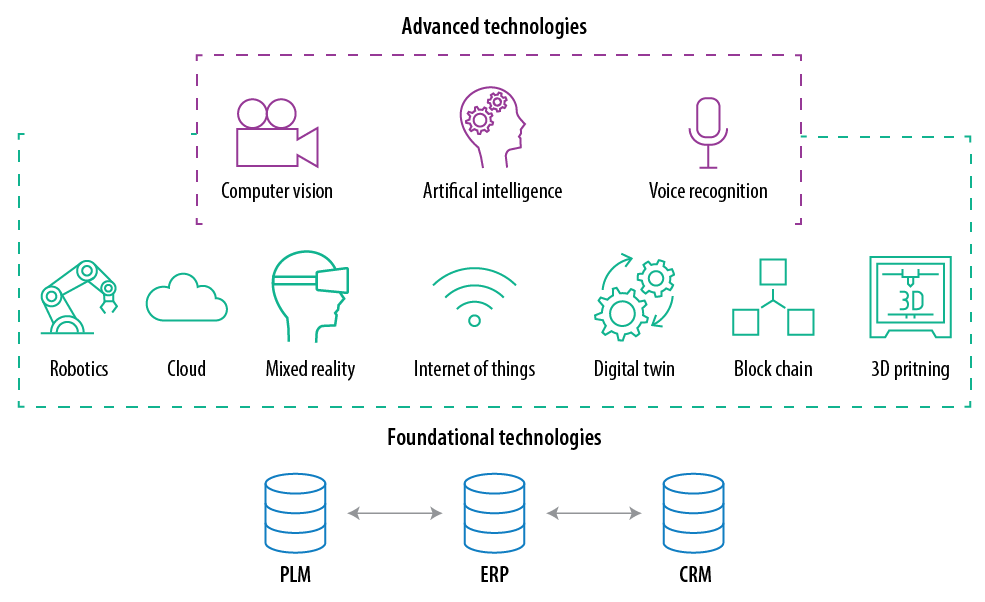
Source: Infosys Knowledge Institute
Safe handling of bulky systems
Inspection of bulky aircraft parts is time-consuming and prone to human errors. At times, handling parts and moving them across the shop floor pose safety concerns for workers. Usage of autonomous vehicles combined with robots, computer vision, and image analytics can assist humans, minimize errors, and reduce time to inspect large aircraft parts. Lufthansa Technik has deployed a swarm of drones for major system inspection, reducing the time taken by 75%. It also uses mobile robots for fuselage inspection. General Electric makes extensive use of snake-arm robots for engine inspection and maintenance.11
However, the changes required in shop floor layout to implement autonomous vehicles and robots present a challenge. Automatic obstruction detection and avoidance in robots make it a costly solution if dedicated lanes are not laid out on the MRO shop floor.
Confluence of technologies
Emerging technologies need to integrate and converge toward a common objective to deliver maximum results. Industry 4.0, or the Fourth Industrial Revolution, advocates transparency, technical assistance for simulation and decision-making, and autonomous decisions where possible. Optimizing the usage of machines, keeping track of various items of floating hardware on the shop floor, and having a bird’s-eye view of the complete MRO shop are key requirements today. Adopting the principles of Industry 4.0 can help ensure the continuous check of machinery, predict the failures of the machines well in advance, plan the maintenance at an optimal time, and keep track of various hardware across MRO shop floors.
The MRO industry is the last mile in the aircraft lifecycle. It plays a key role in sustainability, using advanced technologies for end-of-life management of critical parts
Recommendations
The MRO industry needs an effective automation strategy to digitize various operations, enhance sustainability, and train employees to develop the necessary skills. Automation of physical and digital workflows integrated with human capital can simplify complex processes. Technologies that help train humans and assist them in decision-making will be important to choose and invest in.
MRO systems and processes need to be reengineered with sustainability in mind, keeping track of the genealogy of parts and reusing them. Sustainability is essential not just to save cost but also to reduce carbon footprint. As part of sustainability, circular commerce will enable the reuse of valuable materials where possible and beat the inflation in their market prices.
The matrix below shows a range of technologies for MRO-specific use cases. The MRO industry is the last mile in the aircraft life cycle and plays a key role in achieving sustainability. That said, the latest technologies covered in the above sections have the potential to modernize MRO operations and advance airline efficiency.
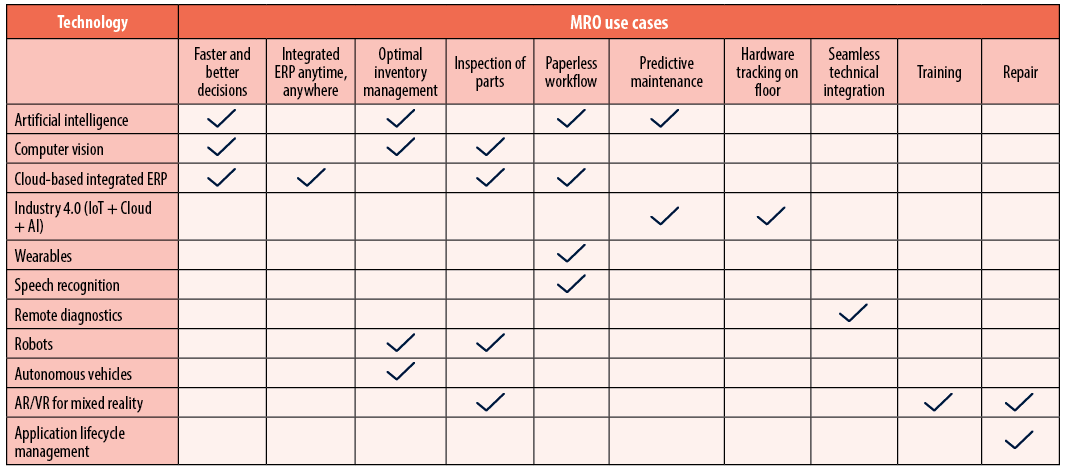
References
- Where next for air travel?, January 22, 2022, The Economist.
- MRO 2025 - identifying opportunities to accelerate growth, 2018, Frost & Sullivan.
- Global fleet & MRO market forecast 2022-2032, Brian Prentice and et al., February 2022, Oliver Wyman.
- Aerospace manufacturer transforms manufacturing with a smart factory ecosystem, 2022, Infosys.
- The industrial metaverse: Where simulation and reality meet, Danny Lange, January 26, 2022, VentureBeat.
- Smartening up with Artificial Intelligence, April 2017, McKinsey.
- Volotea MRO Modernization in AWS, Volotea MRO Modernization in AWS, Albert Capdevila and Alfonso Simó, November 29, 2021, Amazon Web Services.
- Twinning Digital Twins Show Their Power, Louise Bonnar, May 16, 2020, Aviation Maintenance.
- Best practices for component maintenance cost management, December 2015, International Air Transport Association.
- Rolls-Royce launches first immersive virtual reality training for business aviation customers, May 13, 2020, Rolls-Royce.
- Flying, clinging and crawling – using robots in MRO, Bill Read, April 02, 2019, Royal Aeronautical Society.