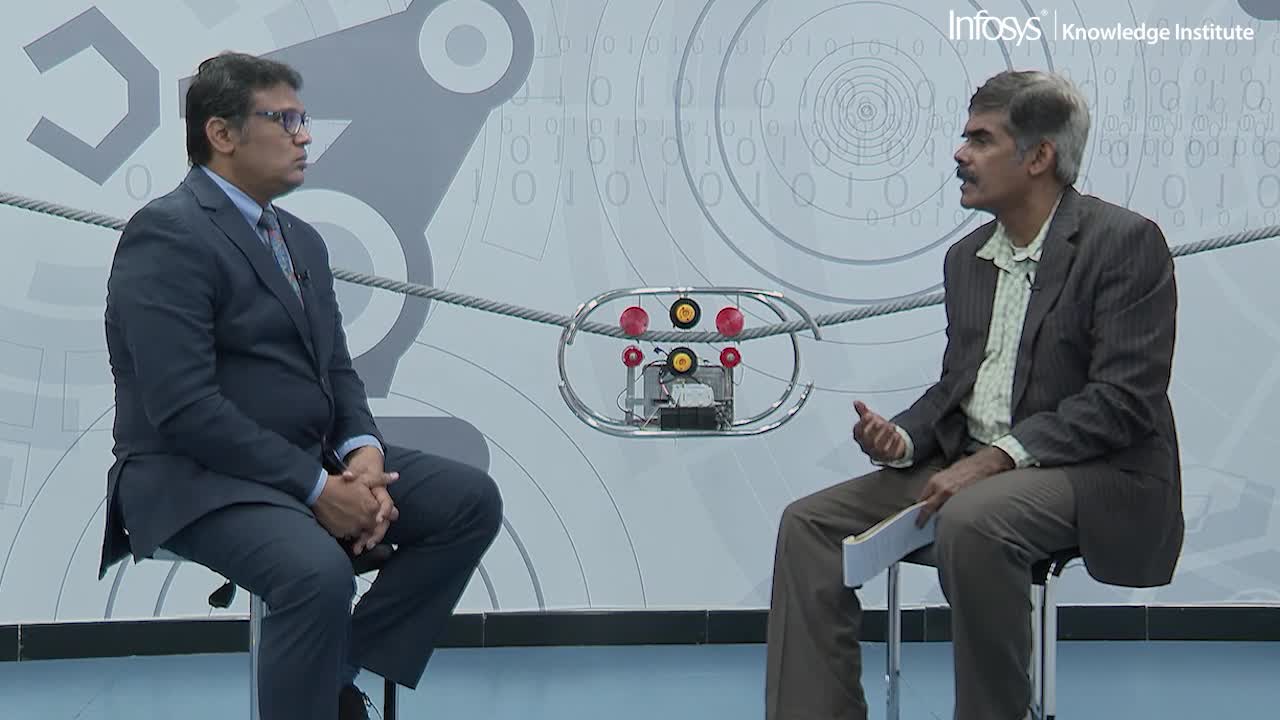
Materials innovation and design enabled by 3D printing
Prof. Shanmugam Kumar talks about emerging trends in 3D printing or additive manufacturing and how it enables materials innovation and new product design. He leads the Advanced Materials and 3D printing lab in the James Watt School of Engineering at the University of Glasgow. His research interests revolve around mechanics, materials design and innovation, and 3D printing.

Ramachandran S: Hello everyone. My name is Ramachandran. I lead engineering and manufacturing domains in Infosys Knowledge Institute. Today we are privileged to have with us Professor S. Kumar.
Professor Kumar leads the Advanced Materials and 3D Printing Lab in James Watt School of Engineering at the University of Glasgow. He obtained his PhD in Solid Mechanics and Materials Engineering from the University of Oxford. And his research interests revolve around mechanics, material design and innovation and additive manufacturing.
Today we are going to talk to him about emerging trends in additive manufacturing and how it drives innovation in materials engineering and design.
Professor Kumar, there has been a lot of talk about 3D printing in the past few decades, but do you think the moment has finally arrived? In your experience, do you see large-scale adoption of 3D printing in the industry?

Prof. Shanmugam Kumar: 3D printing, also known as additive manufacturing, has indeed seen significant advancements and adoption across various industries. While it has been a topic of discussion for decades, the technology has reached a point where it is increasingly being used for innovative applications.
In recent years, 3D printing has been used for rapid prototyping, enabling engineers and designers to quickly create physical models of the designs. This has greatly reduced the time and cost record for product development cycles.
Additionally, 3D printing has found applications in the production of customized or complex parts that are challenging to manufacture using conventional methods.
Industries such as aerospace, automotive, healthcare, architecture, and consumer groups have embraced 3D printing for various purposes. For example, in aerospace 3D printing has been used to create lightweight, complex parts, reducing weight and improving fuel efficiency.
In healthcare, it has been utilized for creating personalized medical implants, prosthetics, and even organs.
Furthermore, the availability of more affordable and user-friendly 3D printers has facilitated adoption by small businesses, hobbyists and individual consumers. This has led to a growing maker community and increased experimentation with 3D printing.
While 3D printing has made significant strides, it is important to note that certain challenges still exist. These include limitation and material options, print speed, scalability, and quality control. However, ongoing research and development efforts are addressing these challenges and pushing the boundaries of what is possible with 3D printing.
In action, while 3D printing has been a topic of discussion for many years, it has indeed reached a stage where it is being adapted on a large-scale for innovative application across industries. The technology continues to evolve and its impact is expected to grow as advancements are made in materials, processes and scalability.

Ramachandran S: Thanks, Professor. You spoke about challenges faced by 3D printing. So what do you see as a tipping point for large-scale adoption of 3D printing? Is it the cost of the equipment itself? Is in the operating cost? Is in the human talent? Which of these factors do you see becoming a tipping point where we'll see large-scale adoption of 3D printing?

Prof. Shanmugam Kumar: It is indeed an interesting question. The tipping point for large-scale adoption of 3D printing can be influenced by multiple factors including cost, human talent, and technological advancements.
Some key considerations are cost-effectiveness, material advancements, scalability and throughput, design and engineering capabilities, skilled workforce, standardization and quality control, and demonstrated value and success stories. It is important to know that these factors are interconnected and intertwined, and advancements in one area often spur progress in others.
The tipping point for large-scale adoption will likely occur when a combination of these factors aligns making 3D printing more accessible, cost-effective and capable of delivering value across a range of industries.

Ramachandran S: Professor, 3D printing has really grown beyond rapid prototyping into real-life applications. So can you give us some examples of impactful use cases where it is used most where you have seen most impact from 3D printing?

Prof. Shanmugam Kumar: As 3D printing technology continues to advance, several popular use cases are emerging that have the potential for wide adoption across industries. Some notable examples are customized in personalized products, spare parts in localized manufacturing, complex geometries and lightweight structures, tooling and jigs, medical applications, education and research, and sustainable manufacturing. These are just a few examples and the applications of 3D printing continue to expand across industries.
As the technology matures, become more cost-effective and materials and processes improve, we can expect to see even wider adoption in diverse sectors.

Ramachandran S: So, traditional manufacturing has usually produced homogeneous parts, but 3D printing has a capability to produce locally anisotropic or heterogeneous parts which have multiple mechanical properties as a function of location or even time. So can you share some examples of such heterogeneous parts?

Prof. Shanmugam Kumar: 3D printing has the unique capability to create parts with local anisotropic and heterogeneous characteristics where different areas of a printed object can have varying mechanical and functional properties. This ability is often referred to as gradient printing or functionally graded materials, and it is a distinguishing feature of additive manufacturing.
So, there have been numerous applications that leverage this capability to create parts with tailored properties. So some examples are biomedical implants, aerospace components, energy applications where we create materials for batteries, supercapacitors and fuel cells, and other mechanical parts which are meant for mechanical energy absorption, like cellular structures for crashworthiness and so on.
So there are other applications such as the thermal management, morphing structures, acoustic materials, EM machines, and stealth technology sensing and camouflage materials. So the ability to create parts with local anisotropic and heterogeneous characteristics is indeed a unique selling proposition for 3D printing, it opens up new possibilities for designing and manufacturing complex structures with tailored properties that are difficult or impossible to achieve using traditional manufacturing methods.
This capability can lead to improved performance, enhanced functionality, and increased efficiency in various industries.
It is important to know that while 3D printing offers this advantage, it also poses challenges in terms of design optimization, material selection and process control. Achieving consistent and reliable gradient properties across a part requires careful consideration and expertise in design and manufacturing.
Nonetheless, the potential benefits make it an exciting aspect of 3D printing and a key factor in its continued adoption and development. For example, in our own group, we explore pretty much multifunctional and multi-material 3D printing technologies where we design cellular materials at different lengths, introducing spatial material gradients and spatial geometry gradients to enhance macroscopic structural and functional properties.

Ramachandran S: That is very insightful, Professor. Very interesting examples you gave. So you covered a diverse set of industries. So a few short questions for you. So if you were to pick, which industry, one or two industries, would you see most adoption of 3D printing in the short to medium term?

Prof. Shanmugam Kumar: So it's challenging to pinpoint a single industry that will see the most impactful adoption of 3D printing as a technology's potential impact extends across various sectors. However, industries such as aerospace, healthcare, defense and automotive are already experiencing significant advancements and adoption of 3D printing, making them strong candidates for impactful adoption in the future.

Ramachandran S: Also spoke about the human talent. So what would be your suggestion for professionals who are interested in learning 3D printing, what is the best way to train themselves to pick up skill sets in 3D printing?

Prof. Shanmugam Kumar: Yes. Professionals should learn design for additive manufacturing to fully capitalize on the capabilities of 3D printing. The best way to learn this technology is through a combination of specialized training courses, online resources, workshops, and practical experience with 3D printing technologies and design software.

Ramachandran S: So, enterprises today are undergoing digital transformation. How do you see the role of digital transformation in approval and certification of 3D printed parts, specifically in regulated industries like aerospace? How do you see the role of digital transformation?

Prof. Shanmugam Kumar: Yeah, it's a big question. I'm not sure if I can answer it in one or two lines, but let me try to answer this as quickly as possible, crispy as possible.
Digital transformation in enterprises plays a critical role in facilitating the journey of 3D printed enabled innovations and obtaining quick approval and certification for use, particularly in the highly regulated aerospace industry.
So this is how it helps. Digital design and simulation tools, digital documentation and traceability, enhanced collaboration and communication, digital trends and virtual validation, data analytics and machine learning.
In fact, digital transformation enables a more efficient and streamlined journey for 3D printing enabled innovations in the aerospace industry by leveraging advanced design tools, digital documentation, collaboration platforms, virtual validation techniques, and data analytics. It enhances compliance, reduces time to market, and facilitates the necessary approval and certification processes.
So for example, in my own group, I primarily lead 3D printing group, which focuses on development of materials, but then under the broader umbrella of smart manufacturing or digital manufacturing, we are trying to connect everything right from feedstock synthesis to in-product by digital trade and involving AI and ML tools. So AI and ML facilitate not only in the development of products, but also the designer processes, even in the monitoring of the processes and so on.

Ramachandran S: Thank you so much for taking your valuable time to answer our questions. We really appreciate that.

Prof. Shanmugam Kumar: Thank you so very much, and it was a pleasure seeing you here and being a guest to the Infosys, a wonderful center.

Ramachandran S: Please visit infosys.com/iki. Keep learning, keep sharing. Thank you for watching this show.