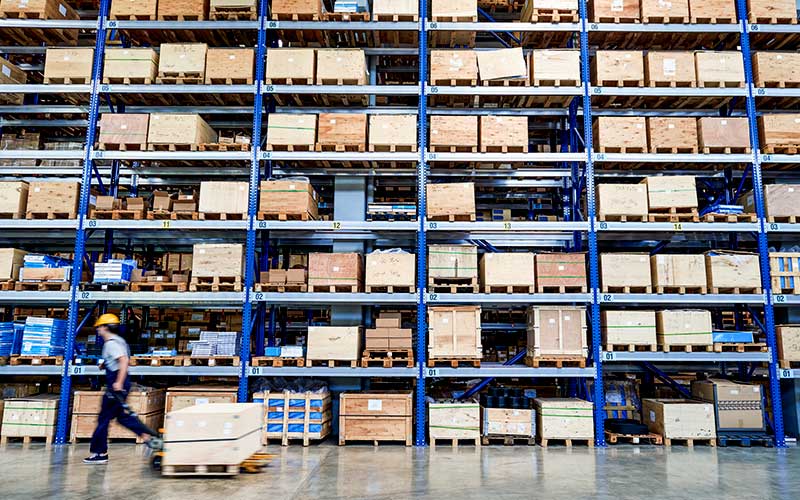
-
Dr. Mohan Gopalakrishnan on Supply Chain Risk and Management
11 Aug 2020
-
Dr. Mohan Gopalakrishnan (his students call him Dr. G!) is the Department Chair, Supply Chain Management in the W. P. Carey School of Business at Arizona State University. He discusses how supply chain planning and resilience has become even more relevant in today's COVID environment, and how solid supply chain practices can be applied across all aspects of service, including nonprofits.
Hosted by Jeff Kavanaugh, VP and Head of the Infosys Knowledge Institute.
“I think the important thing that we've all learned in [the pandemic], and that's probably the number one thing is visibility, and increasing visibility. That's almost become a cliché, but it's the truth.” Dr. Mohan Gopalakrishnan
Show Notes
-
00:47
In a time of historic disruption, what part of your research is especially relevant now?
-
02:52
Jeff introduces Mohan
-
03:16
What inspired you to pursue your academic path in the area of supply chain and in academia overall?
-
04:33
How did you gain expertise specifically for supply chain?
-
07:55
Can you talk about your approach and what you've seen, be successful defining, describing, and learning to live with risk?
-
10:33
Why is it that these problems are still there when I was with executives 20 years ago, addressing these things? Why do they still persist?
-
12:09
I think the nature of its cumulative. Like you said, evolving, you've had considerations that just the demands weren't there as much before. And of course, sustainability as well as a valued dimension has really come to the forefront.
-
13:34
Noticed you did some work with the Saint Vincent de Paul Society. Could you talk about what that project or initiative was and what you gained from it?
-
19:58
Can you talk about the conflict between local and global optimization for supply chains?
-
23:16
Can you highlight maybe a disconnect between the needs we have now and the structures in place, and some steps executives can take to navigate their way through it?
-
26:07
What are three things that executives, leaders, can do to increase resilience in their supply chains?
-
28:33
What's a good example of somebody who's really doing it right?
-
30:23
For the young person who's considering careers and maybe looking at supply chain, what is your advice to them as they're thinking about supply chain and risk management things they can be thinking about for the next 10 or even 20 years to maybe put their heart and soul into as a career?
-
32:21
What are the books or people that have made a big impact on you?
-
33:23
If we could swap seats and you could choose someone to interview for a podcast, who would you choose?
-
34:01
Any online resources you recommend for further learning?

Jeff Kavanaugh: In the words of Elon Musk, “the supply chain stuff is really tricky.” Even in relatively benign 2019, global losses due to natural disasters came to $150 billion. In 2020, COVID-19 had the global system flashing on red, damaging global trade at an unprecedented speed and scale. Initial supply shock, followed by demand shock revealed the vulnerabilities of complex global supply chains with all of us facing the challenge of receiving basic products and materials. The call to action is direct and emphatic to negotiate the path between convenience and catastrophe, we need stronger, smarter, more resilient, and diverse supply chains. Mohan Gopalakrishnan, you are Department Chair of Supply Chain Management at Arizona State University. In a time of historic disruption, what part of your research is especially relevant now?

Mohan Gopalakrishnan: Interestingly, the current pandemic has as you rightfully said, led to two things I think in the supply chain. One is posturing, the other is repurposing. And most of the supply chain managers are looking at these two basically to better coordinate the challenges in supply and demand. Three parts of some of the things that I've done, and I'm going to quickly talk about that and we can dwell on them later on, one is the healthcare hospital supply chains. Unprecedented types of demands that they have seen that they have not faced and this has been global, especially in the emergency room. The sourcing departments have been working around the clock and interesting innovations have gone into keep the shortages low, and keep the operations going forward.

Mohan Gopalakrishnan: One of my research that has really played an interesting role that I'm observing right now is a reverse logistics believe me or not. A thing that is not that sexy a term or something that you hear in supply chain. An example there is refurbishing ventilators. The second one is what I call as hidden supply chains, or newer supply chains that emerge. As companies come back and try to get to some sense of normalcy, they have to run a healthcare supply chain, even the commercial ones, to keep their environment safe. That is an interesting challenge to many supply chain managers who are not used to running such supply chains.

Mohan Gopalakrishnan: The last one from my research that's relevant is how the humanitarian supply chains have come to the brunt force. They've come forward in order to minimize any wastage in the supplies and coordinate better with the mouth that needs to be fed or the people that need help. These are the three areas that I think of my research that bears upon as we move forward facing this pandemic.

Jeff Kavanaugh: And supply chain and risk management is what we'll be exploring in today's conversation. Welcome to the Knowledge Institute Podcast, where we talk with experts on business trends, deconstruct main ideas and share their insights. I'm Jeff Kavanaugh, Head of the Infosys Knowledge Institute. And today we're here with Professor Mohan Gopalakrishnan, or as he's affectionately known, Dr. G. Mohan is the Department Chair of Supply Chain Management at Arizona State University in the W.P. Carey School of Business. Mohan received his PhD in Management Science from University of Alabama in 1992. His research interest include global supply chain risk management, health care operations management, and nonprofit humanitarian operations. Mohan, thanks so much for joining us. First of all, what inspired you to pursue your academic path in the area of supply chain and in academia overall?

Mohan Gopalakrishnan: To some extent, though I could use the cliché, destiny, I think a series of events. I was not planning to come into academia, I was wanting to work in the industry. I was pursuing a career in engineering when I ran into certain issues in the part of the world that I grew up as it opened up the global trade that exposed the inadequacies of my knowledge. I wanted to pursue higher studies and reach a better place so I moved to the United States to pursue my master's. Again, wanted to stop at the master's level and go back to work. But as you're going through in academia, you get exposed to what I call as experimentation.

Mohan Gopalakrishnan: I used the mathematical toolkit as my experimentation as I was going through my masters. And then I was doing it in pure engineering when I got an exposé in this part of the world with the business schools and primarily to economics and production systems. That kind of drew me towards studying more and before you know, one thing led to the other. Finishing up my PhD, and looking back, I wanted to continue my journey in the academic pathway and that's what led me to this.

Jeff Kavanaugh: That was a moment of truth that made an impact on you. How did you gain expertise specifically for supply chain? Especially for those out there who are trying to develop that next level of sophistication or academic rigor, what is it that contributed to your depth in it?

Mohan Gopalakrishnan: A multitude of things I would say. I don't think when I started my career back in India, or when I came here to Alabama, supply chain was not even a term that was coined at that point in time. I was exposed mostly to my engineering education to manufacturing world. And as I was working in India, India was opening up to the global trade, and the first automotive industry that came in was Suzuki from Japan. And with them came the stringent quality requirements. I clearly remember my first shipment of a product that I designed and was helping to manufacture and ship to Suzuki as a supplier was completely rejected, and the bubble bursting kind of a moment. And I was asked to come to the Suzuki plant and was given no help. And I had to figure out what was wrong with my particular product and fix it. And these were 2000 of the units that I had to, by hand, fix certain things.

Mohan Gopalakrishnan: I learned building quality versus inspecting quality the hard way. That moment taught me about the inadequacies that I was talking about. I was not prepared to lead manufacturing systems without understanding their intricacies. That was my first foray. And along the way I understood that it's not just within the four walls, it's an end-to-end supply chain that has to be orchestrated in order to get anything done properly. The training that I received later on helped me understand the cost of systems and the trade offs. Those are important things as you're looking at supply chain and trying to manage them. And as you look at trade offs comes how you manage and mitigate risk. That's the second thing that happened. And over the time as I was getting trained, I was also constantly being exposed to the information systems and information technology. That was a way to better connect and understand and enhance the visibility in supply chains. That was my third learning.

Mohan Gopalakrishnan: And the fourth one was to do with people. We thought people, you're going to have supply chains. People in this case mean long term relationships and how do you study the motivation and incentive systems, and last but not the least with relating to the people is something that's again, in supply chain literature, you don't see in the top 10 kind of publications, which is supply chain finance. Gates Foundation once said, "We can pour all the money into developing nations, but unless we improve the working capital of small suppliers, you're not going to get a healthy supply chain that's going to work with all firing on all cylinders. The supply chain finance is another area which I have come across and have tried to understand and use that in my research. These are some of the things that I've seen as I grew myself in this field.

Jeff Kavanaugh: That sets the table nicely for us, several topics because these are top of mind for supply chain leaders today, especially given the pressures exerted with COVID and the aftermath. Let's talk about risk for a little bit. To the uninitiated, risk can appear to be something you want to avoid. I want to prevent risk. You used the word, though, “mitigate,” instead. Can you talk about your approach and what you've seen, be successful defining, describing, and learning to live with risk?

Mohan Gopalakrishnan: One way to look at it, which I'm not saying anything, people and managers have been looking at risk, is the frequency of occurrence of a risk and its impact. That's one way of categorizing risk. A forecast error might have high frequencies, but depending on how long the forecasting happens, the impact could be mitigated by shortening the duration of forecasting or lengthening it depending on type of industry. That is one way of looking at it. The other way of looking at it is not just your part of the supply chain, but actually the complexities increase as you go deeper and deeper into your suppliers. Companies like Resilinc is now coming in and telling us, "Let's map the supply chain and actually understand that the vulnerable part might not be where you think there's the top tier or the first tier supplier, or it could be a fourth or fifth tier supplier whose value added in this might be very less compared to other parts of the supply chain, but if they go down the impact on the overall stoppage might be much higher."

Mohan Gopalakrishnan: On our the way of looking at this mitigation, this mapping and understanding the supplier of depth and supplier complexity, which is where sometimes it may be as simple effects as looking at the financial health of a supplier. Starbucks was recently talking to me and they were telling us during this COVID, they had a look at the small truck drivers that were moving goods and their financial help was important because initially a lot of the stores shut down before it got open again, and they had to drive through a mechanism. They kept them afloat by making sure they paid ahead of time or they paid even if the services were not delivered. Things of that nature is going to help you mitigate some of the long term risks in developing these kind of relationships. Those are the two ways I'm looking at. One, understand the frequency and impact so that you could have a prioritized way of managing risk. But more importantly, you want to have a mapping of your supply chain and visibility of your suppliers who understand vulnerabilities so that you could come up with game plans to address those.

Jeff Kavanaugh: What's interesting about what you said because I've been in supply chain game for a long time, especially more intensely a while back than today, even in the late nineties with advanced planning and scheduling, capacity planning and integrated with material planning and due date quoting and all those types of things, and network optimization, it's been around for a while. And some of the things you're talking about, those aren't new. Why is it that these problems are still there when I was with executives 20 years ago, addressing these things? Why do they still persist?

Mohan Gopalakrishnan: I think two things. One, supply chains are constantly evolving. That's a good and a bad thing. You don't have a static supply chain 30 years ago towards today. Look at eCommerce as an example, that there's kind of disruptor how flow of groups happen. Flow of information has not remained static either. We've got the demand signals now coming in various modalities, which did not happen 20 years ago. That kind of a constant evolution either from a design part of the supply chain, where from a vertically-integrated to highly-decentralized kind of supply chains to consumer behavior.

Mohan Gopalakrishnan: We've done all kinds of modeling in pandemics, but still look at the toilet paper and its impact. Every pandemic teaches us something new. Supply chains, we've understood are somewhat static in some sense. When an event happens, it's that current design that has to react. We cannot repurpose it very quickly, it takes time. These are some of the reasons I think we constantly look at fundamental pillars of supply chain. Some of which you've alluded to in terms of planning and scheduling and coordination of materials, and understanding visibility better, and using digital information better. That's also a constantly evolving process.

Jeff Kavanaugh: I think the nature of its cumulative. Like you said, evolving, you've had considerations that just the demands weren't there as much before. And of course, sustainability as well as a valued dimension has really come to the forefront.

Mohan Gopalakrishnan: That's a very good point you're making, Jeff. Thanks for bringing that up because I talked in the beginning about reverse logistics. That's a system that is now almost you will design your supply chain for becoming green. And this is an easier part of doing that is, are you designing your reverse logistics? Look at Amazon partnering with companies like Khol’s so that it's easy for customers to return anything so that there is a process that happens in how once the product is handed over, what happens in the reverse flows. That is a part of the supply chain. Again, to make the point that it's an evolving kind of a design that brings anew a problem like forecasting. The forward flow forecasting versus a reverse flow forecasting may not have the same dynamics. That's what makes it interesting to constantly study these things.

Jeff Kavanaugh: Once again, you were listening to the Knowledge Institute where we talk with experts on business trends, deconstruct main ideas and share their insights. We are here today with Professor Mohan Gopalakrishnan, expert on supply chain management and risk. Mohan, you talked earlier about humanitarian supply chains, and preparing for this. Noticed you did some work with the Saint Vincent de Paul Society. Could you talk about what that project or initiative was and what you gained from it?

Mohan Gopalakrishnan: I moved into Arizona about 25 years ago, and I was trying to connect with the society at that time. And one of my colleagues said, "Hey, Saint Vincent de Paul is a soup kitchen. Would you want to come and do some volunteering work?" I said, "Fantastic, let me do that." Went one evening, and we were working in the soup kitchen. I like to understand processes in supply chains better wherever I go, so I started asking questions. "How many such kitchens do you have?" "Well, we have 15 or 20 kitchens here." "Is that the only way food is served?" "No, we have 85 parishes that become locations for serving boxed food or even pantries” and so on and so forth." I said, "Oh, that means there's supply chain. How do you get the supplies coming in?"

Mohan Gopalakrishnan: One thing led to the other, and soon we realized that we wanted to study this and understand. We being my colleague and I, who took me there. As we were looking at this, mostly from an academic standpoint and trying to understand this and also write a small case. That's all I wanted to do is write a small case and take it to the class. But destiny had other interesting plans. The Saint Vincent de Paul was going through an interesting time in the feedings domain. Most of their donations came from grocery chains and there was a heavy consolidation of grocery chains around that time, which is about 22 years ago. And from a million pounds of food that was coming into this reclamation facility that was reclaiming the food and then using it to feed its customers, it was going to go 12 times to 12 million pounds because of the consolidation.

Mohan Gopalakrishnan: The question that the Board of Saint Vincent de Paul looked for was how many more warehouses we have to build to do this reclamation. They gave the question somewhere in March. And I asked him, "How much time do you have before we make a decision?" He said, "We could wait for about three months." I said, "Don't make any decision, just wait for three months." It was summer, so it was an apt time. We put a bunch of students and we started working rigorously, looking at supply and demand kind of a thing. It was the most complex supply chain. And then when I went and I said, "Oh, what is the food supply chain going to look like?" But demand uncertainties are so difficult to predict. You can use a index like poverty and zip codes to find out how many people need food, but it's not an exact science.

Mohan Gopalakrishnan: Supply is the same way. It comes in fits and starts kind of a thing from grocery chains and donations and things. The coordination of supply and demand leads to times where the amount of food that's available is in excess of the capacity to store. And other times it's not there, the storage facility is empty. How do you play this game? We started putting together ideas and game plans. To move the story forward, they have not built an additional warehouse. We were able to smartly manage this entire supply chain by bringing ideas from the for-profit supply chain into this nonprofit world. Here's a classic example. Every day, the food was picked up from this main reclamation warehouse by people from the parishes. They would come at their own time when they could come with a small truck and take whatever they want. The outflow was not consistent. The outflow did not keep up with what the food requirements of the parishes were.

Mohan Gopalakrishnan: We did a cross docking model. Saint Vincent de Paul sent out its own trucks every day to pick up donations like furniture and other things from its customers. There was an outbound truck route and it's outbound, it was empty. Inbound it brought the furniture. The outbound, we started loading up with food and we started designing, centralized, along the routes where parishes could cross dock their trucks and pick up food almost on a day-to-day basis. This kind of ideas from a for-profit pool coming to the nonprofit, when we started this project, two things were striking to me. Number one was the growth in supply that was going to come in. Second, the food that was wasted because of the expiry dates and things at that time was at 25%. One-fourth of the food donated was actually wasted.

Mohan Gopalakrishnan: By the end of this project, which took us about two or three years to complete it, we brought it down to about 6 to 7% wastage. We did not build an extra warehouse, and even today, it stands there as an interesting case study as to if you manage your supply chains properly and coordinate supply and demand, you could achieve the efficiencies and meet the purposes.

Jeff Kavanaugh: Thanks for that inspiring as well as insightful update. And I wanted to highlight that because I am familiar, growing up, working with Saint Vincent de Paul in my local area, and I think it's a good example of a few things. First of all, for those of you, aren't aware Saint Vincent de Paul was actually a Saint back in France and originated this humanitarian organization. That because it was a good idea, and essentially the church put it out in a lot of places around the world, it became local community. Soup kitchens, stores for reclaimed furniture, or resold furniture. Basically serving the needs of the local population and yet it was loosely strung together across a community or an organization worldwide. And what's interesting here is in an era where stakeholder capitalism is now becoming the mantra, it highlights that it's not all on the corporation to do it.

Jeff Kavanaugh: The ideas can be shared with some of these non-government organizations who are trying to do it, they're just not equipped to do it as much. And it isn't just money. In this case, it's ideas and taking some action. And I think this is a highlight, if I can use the phrase “supply chain for good.” Applying these concepts, and I want to reiterate that point 25% food wastage down to 6%. You apply that on a regional national and global scale, a whole lot of problems we have don't require more funding, but they do require some action and some ideas. Thanks for sharing that. One of the problems with global supply chain anything is managing the conflict between what works locally and globally. Can you talk about the conflict between local and global optimization for supply chains?

Mohan Gopalakrishnan: Well, it is playing out so well right now in this COVID pandemic, I want to use the word national versus local as an example before we go even global because lack of centralized visibility, more than anything else into the availability of masks and ventilators, people have to scramble state-wise, county-wise to address their own needs. We know, at least from a supply-chain standpoint, as we start aggregating demand, we can get a better understanding of it. As you get a visibility in a more centralized way, it's the hub and spoke kind of a system that have worked very well. Everything is consolidated. We know the demands and then the distribution happens in a more decentralized way. Lack of that is the necessity for safety stocks at many levels. That has an impact in terms of how you handle variability. In the initial stages in New York City, in the coordination of the health related supply chain for managing COVID, especially the ER, it was all trying to do what's best for New York City.

Mohan Gopalakrishnan: But soon it became clear that the tri-state area had to coordinate their own actions together for better outcomes because one place had more ventilators or masks, the other places needed it, so this kind of a coordination really paid off. We at ASU worked with an organization that was doing this. It's called ALAN. It's America's Logistic Aid Network, ALAN. What we were trying to do was look at this consolidation or aggregation of demand across the country actually. But from ASU, we got a couple of states. One was in the tri-state area, one was in Tennessee, and then we were looking at how do we coordinate. To answer your question, anything that we could do, where we could have a more aggregate look at things helps us plan better, but then the logistics aspects of it has to be optimized to locally take care of the demands.

Mohan Gopalakrishnan: That's how I look at it. Whether you put it nationally, now you move globally, the complexities just increase. The locational issues and the lead time issues exasperate as you go more global, but the options also are available. For example, when Wuhan shut down, we were told that the neighboring states started pitching in for some of the manufacturing capacity, but the logistics network was down completely. They had to ad lib some of these things to a Russian railway network and move to Russia, back into Europe, in order to distribute. People are really resilient in terms of how they find solutions in order to get things done.

Jeff Kavanaugh: Let's take that one step further and give a little more into thorny issues here. What about the disconnect? You talked about operationally- getting it done. Then there's the disconnect or maybe misalignment between the need, the problem and the current structures including whether it's political or financial or labor that actually can solve it. Can you highlight maybe a disconnect between the needs we have now and the structures in place, and some steps executives can take to navigate their way through it?

Mohan Gopalakrishnan: I want to look at this toilet supply chain as an example to answer this. The disconnect was not because of any particular financial or political issue, but it was a structural issue in the supply chain. Supply chains had a dual purpose. They had the commercial purposes in the toilet issue and also the retail part of the supply chain. Both had very different manufacturing assets deployed, logistics assets and demand patterns. Now, when one shut down, which is the commercial side of things, and the other one just took off because of panic buying and whatnot, the misalignment did happen only because the structure was so different between the two of them. And it's a big shift to turn overnight, to get things in the manufacturing side to reduce the size so that it could fit the commercial side or the logistics that had to be more frequently delivering, as opposed to infrequently in large quantities on the warehouse, and their impact on these things had to be readjusted. There was misalignment, it was a structural issue, and then it had to be corrected. It took a while, but then people figured it out.

Mohan Gopalakrishnan: Now, let's look at from a national or international perspective. This is a unique pandemic because this is teaching us that globally, everybody is affected at the same time. People are protecting their assets so that they could take care of their own citizens. That nationalistic forward is going to have impact. This is an example. Cisco was telling us that they were moving goods in India, and they had gotten permission during the shutdown to move a few things so that from there, it had to be shipped to China to meet demand, but then the local governments in India looked at it differently and stopped movement. Because of that, a global supplier like Cisco was hampered because they couldn't move things and they had to politically maneuver this in order to get things done. That's an interesting example. They had gotten the permission, they knew what they were doing, but the local political climate said, "Why are you moving these goods outside when it may be needed inside?" That's a challenge that we are facing, which has to be dealt with once we've reached a little bit of a normalcy.

Jeff Kavanaugh: Dealing with the topic of resilience, because in some respects, that's the other side of the coin of risk. One is you're mitigating and you're accounting for risk. The other is you're being resilient so matter what comes at you, you can accommodate it. What are three things that executives, leaders, can do to increase resilience in their supply chains?

Mohan Gopalakrishnan: I think the important thing that we've all learned in this, and that's probably the number one thing is visibility and increasing visibility. That's almost become a cliché, but it's the truth. Is do I know where my vulnerabilities exist? And what are my options if a pathway shuts down? Understanding that and building for it because the move today is towards a different type of resiliency, which is questioning all the efficiency-based improvements we have done and saying, let's have a lot of inventory in the local kind of a scenario as a buffer, but that would probably serve the short run. In the long run, it may lead to other inefficiencies in the system. Understanding the visibility is a critical part of this journey that we are looking at.

Mohan Gopalakrishnan: I think the second one, this is something I've learned talking during these times to supply chain leaders. We at ASU have a strong board of supply chain leaders. The who's who from Amazon who Dell to Starbucks and Cisco and so on. And they have all been telling me that this whole idea of repurposing the supply chain has become a critical one. A particular location or a particular thing has to now be more self-reliant than a being dependent. How do you look at dependencies and what can you do when you want to let somebody temporarily disband in their dependency and operate on their own? Now I'm speaking with both sides of the mouth. I'm saying don't do a lot of buffering. For removing the dependency short run, you may have to have a lot of inventory for helping that particular local environment to survive. Could you build that locally and do that? The second one is the dependency studies and how you want to look at it.

Mohan Gopalakrishnan: Of course, the third one is adaptability to the changing needs. You may call it agility, some call it flexibility. You want to constantly look at these types of issues in your supply chains to see how flexible you are. As the example I gave from Wuhan and moving goes to Russia in order to move them to Europe, how flexible and adaptable you are to restructuring your supply chains. Those are the three things that come to the top of my mind as to what people are at least currently doing to address the resiliency.

Jeff Kavanaugh: What's a good example of somebody who's really doing it right?

Mohan Gopalakrishnan: That's a tough one. I think people are doing very, very different things. I would rather say that's a better way of looking at it. How are people handling it? There has been some failures. People have not been able to get the products on time, which has delayed... Even Dell, as an example, said they did the best they could, but their lead time shot up from certain products from three days to three weeks, or even more than that. The reason is the demand for some of these products have seen some unprecedented levels because of people working from home and all those kinds of things. Most of them have tried to adjust to this new normal and tried to orchestrate their supply chains. Now, one company that was interesting to me, I don't want to call it, “they did it the right way,” or in that sense, but I want to say how they repurposed.

Mohan Gopalakrishnan: This is a company called Bloom Energy. It's located in Silicon Valley. It does alternate energy kind of products, a fuel service. When the California government asked for companies to step in and help out to provide more medical supplies, this company repurposed the supply chain to look at refurbishing ventilators and supplying it. They built the supply chain within a week and were able to supply close to about 300 to 400 ventilators in record time. Even though the company had shut down, the employees came back and put their heart and soul into this in order to send the products in the right time, because you are talking about the first wave in March when California was peaking, and that's what happened. I could say that was an interesting example that I observed.

Jeff Kavanaugh: For the young person who's considering careers and maybe looking at supply chain, what is your advice to them as they're thinking about supply chain and risk management things they can be thinking about for the next 10 or even 20 years to maybe put their heart and soul into as a career?

Mohan Gopalakrishnan: What I tell my students, Jeff, is continuous learning. That's the mantra now. As people become alumni today, after they've completed a degree, our biggest challenge is keep them connected. The digital technologies help us to some extent. Posting information on a daily basis and making people comment. More importantly is this pandemic has started how we can connect digitally and people will make the time, even if they cannot by traveling. I would say to all the young people who are thinking of a career in supply chain to be constantly connected.

Mohan Gopalakrishnan: The second thing that I've learned is there is the generation gap in supply chain. As I'm talking to my board, they are constantly asking me, "How do I involve more women? How do I involve more millennials in supply chain?" And there's building the bridges between generations. One, which has interesting knowledge base, the other, which is extremely resilient in place as the younger generation. How do you connect them? And the lesson to the end of generation that's going out is be connected to the other generation so that you will benefit. And the third area is analytics is almost becoming the sliced bread today. Who in business school would talk about blockchains? Anybody. HR departments are talking about blockchains. That type of an interest in this analytics area is something that I want our next generation to constantly pay attention.

Jeff Kavanaugh: Excellent advice for young people of all ages.

Mohan Gopalakrishnan: That's true.

Jeff Kavanaugh: What are the books or people that have made a big impact on you?

Mohan Gopalakrishnan: Well, The Machine That Changed the World kind of changed me. When I came into this part of the world as a student to study, my professor gave that book to me and I had just come out of MIT Press, and I was fascinated in the lean area where I made a career for a while. That book, I think still, you want to go back and read it in the current context. Some of the books that we know, Peter Drucker's books and Michael Porter's books, all these books on strategy and tactics, we want to reread them to understand how the world has changed. The second kind of an area that I want people to read, they can look up for books are total cost in the supply chain. And sometimes if that's a course that I teach, it's not one of those courses that look pretty interesting, but it is filled with details. Cost to serve your customer. Things of that kind. Anything to do with that and books on analytics is also a good one to look at.

Jeff Kavanaugh: If we could swap seats and you could choose someone to interview for a podcast, who would you choose?

Mohan Gopalakrishnan: Can I choose two people?

Jeff Kavanaugh: Yes, you can.

Mohan Gopalakrishnan: And I wanted them to be in a panel? Jeff Bezos and Jack Ma. Alibaba and Amazon. It would be fascinating to see the way they have developed and the way they have revolutionized the world. I travel across the globe a lot and when I go to my hometown now in India where I grew up, I can't recognize it because Amazon has bought up almost 30% of the land and has developed it. And this is amazing as you look at these two companies and how they have developed.

Jeff Kavanaugh: Any online resources you recommend for further learning?

Mohan Gopalakrishnan: The Knowledge@Wharton is another interesting resource to look at for supply chain and our own W.P. Carey Knowledge is our own podcast and knowledge base.

Jeff Kavanaugh: Yes, you're doing some fantastic things at ASU. And I think that across the board, across multiple disciplines, anyone would be good to bookmark that. And everyone, you can find details for all the books and resources we've mentioned on our show notes and transcripts at infosys.com/IKI in our podcast section. Mohan, thank you very much for your time and a highly interesting discussion. Everyone, you've been listening to the Knowledge Institute where we talk with experts on business trends, deconstruct main ideas and share their insights. Thanks to our producer, Catherine Burdette, Kerry Taylor, and the entire Knowledge Institute team. Until next time, keep learning and keep sharing.
About Mohan Gopalakrishnan
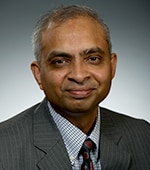
Mohan Gopalakrishnan is an award-winning researcher with a wide range of interests. His work has explored global supply chain risk management, health care operations management, nonprofit humanitarian logistics management, web-congestion and technology capacity management, product design and target costing, pricing and revenue management, “purchase-cards” and inventory management, project management, warehousing and distribution management, and manufacturing planning and control.
His work has been widely cited and published in leading journals, including Journal of Supply Chain Management, International Journal of Production Economics, International Journal of Operational Research, European Journal of Industrial Engineering, International Journal of Information Management, Leadership Quarterly, and Management Science. His projects have been funded by the National Science and Engineering Research Council – Quebec, the Seagram Foundation, and American Express Global Technologies, among others.
His teaching focuses on global operations and supply chain management, business process excellence management, lean and Six Sigma management, project management, and technology management. He has won multiple awards for “Outstanding Teaching Excellence.”
Before coming to ASU in 1998, he held a faculty position in Decision Sciences and MIS at Concordia University, Canada, and previously taught at IIT-Chennai, Great Lakes Institute of Management, and IIM-Ahmedabad. He earned his bachelor’s degree at the University of Madras in India, and his master’s and doctorate at the University of Alabama.
Selected links from the episode
Connect with Mohan Gopalakrishnan
- Arizona State University profile
- Email Mohan.Gopalakrishnan@asu.edu
Mentioned in the podcast
- Bill & Melinda Gates Foundation
- Resilinc
- “Amazon And Kohl's: Proof That Collaboration Works” Forbes- May 28, 2019
- The Society of St. Paul
- American Logistics Aid Network- ALAN
- “We’re stepping up to aid the COVID-19 battle; we need your help” Better Electrons: the Bloom Energy Blog- March 30, 2020
- “A Comprehensive List of Books Authored by Management Guru Peter F. Drucker” The Talkative Man- March 19, 2014
- Books by Michael Porter- Goodreads
- Knowledge@Wharton
- Visit the ASU Knowledge site
- Read the W.P. Carey School of Business magazine
- Visit the W.P. Carey School of Business Information Systems Department site for cutting edge technology news and research
Recommended reading
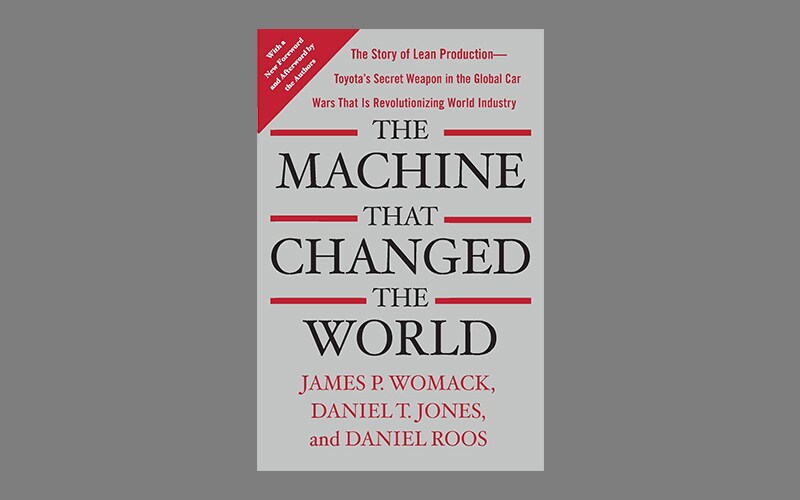