The oil industry has been hit hard over the last few years with high price volatility which saw oil prices plummeting sharply from $100 a barrel in mid-2014 to almost $30 per barrel in early 2016. The prices have since continued to fluctuate in the $40-$75 per barrel range, but given the emergence of electric cars and the increased demand for alternative
fuel sources like wind and solar, it is extremely unlikely that prices will return to previously seen highs.
Oil and gas companies are accustomed to price volatility (see Figure 1 below) and have traditionally responded by managing production, varying capital investments, tinkering with production economics and making prudent operational decisions that impact costs – but, given the complex geopolitical and business landscape of today, these traditional approaches will no longer suffice to build bridges over troubled waters.
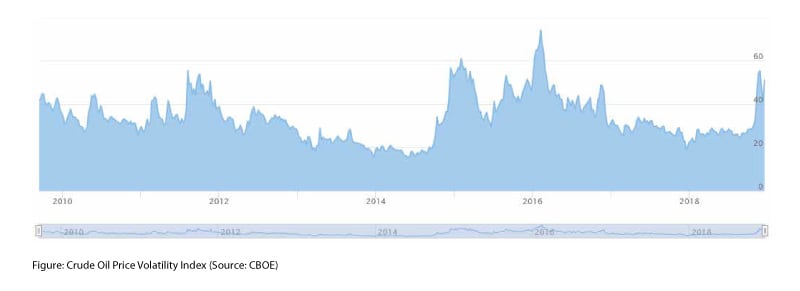
Oil and Gas in the digital age
Oil and gas enterprises are under mounting pressure to adopt innovative methods to achieve cost reduction and hit their efficiency targets. If they fail to do so, it will result in a steady erosion of their margins and a loss of their competitive advantage. There is also an increasing need to knock down the data, process and platform silos that exist within the oil and gas industry. To deal with the challenges companies now face, a holistic strategy is the need of the hour – not a fragmented approach.
Large industries in capital-intensive sectors have traditionally lagged behind high-tech and financial services industries in embracing extreme automation and entering digital era boldly. But even amongst the capital-intensive sectors, we find that the manufacturing, engineering, and mining corporations are leading the way in integrating physical and digital worlds and adopting automation and digital technology.
Oil and gas companies are looking to replicate the Manufacturing success story and ways of working, and Extreme Automation is being increasingly perceived as the missing piece of the puzzle to overcoming their unique challenges.
Understanding ‘Extreme’ automation
Extreme Automation, in simple terms, is about applying available technologies (operation and information technologies) to amplify human potential, accelerate processes and workflows, and magnify the use of systems and tools to achieve improved efficiency and productivity.
It is not about creating yet another application, enhancing one more platform, or automating one manual process. It is about looking at technology in a much broader sense to provide insights, improve the experience, enable innovation, accelerate growth, and assure safer operations.
Many oil and gas firms are already moving to harness this powerful technology. Schlumberger, one of the world’s largest oilfield services company, announced that it had acquired Omron Oilfield and Marine, a company specializing in automation technology and solution.
“It may be hard to believe we’re on the cusp of a technological revolution at a time when the global economy as a whole is slowing… we are indeed entering a new ‘renaissance’ in industrial progress, with the accelerated uptake of cyber physical systems…”
What the tough need to get going: The triple dilemma
Given the recent technological advancements and the choppy waters of price volatility, Oil and Gas majors are in a state of constant
introspection and deep deliberation on how to combat the disruption and challenges. Among many others, the three key questions Oil and Gas industry captains are asking themselves today are:
- Where and how do we deploy capital to maximize shareholder value and improve Return on Capital Employed (ROCE)?
- What should we do to improve operational efficiency without compromising on health, safety and the environment?
- How do we identify ways to improve our supply chain from wells to refinery/re-gasification units to consumers?
Reinforced capital efficiency to make each dollar count
Costs of capital projects usually run into billions of dollars. This creates a huge incentive to improve the execution of capital projects resulting in an optimum balance between cost, time and quality without compromising safety. Large capital projects require a great deal of upfront planning to ensure that all activities are identified and dependencies are accounted for, before breaking ground.
Construction involves multiple niche third parties who work with their own employees or sub- contractors. It is a mammoth task to manage multiple moving parts including personnel, equipment, etc. All this, including tracking of the work being done, progress against plan, continuous risk assessment and mitigation planning, cost management, regulatory compliance, etc., makes it imperative to get things right the first time, safely.
Capital projects are complex and complicated
Capital projects have always struggled with gaps between “as-planned”, “as-designed” and “as-built”. They involve several thousand engineering document deliverables (such as drawings, design documents, procedures and plans) which have to be tracked from concept to completion (and even after handover up through many decades of operations), with the project progress hanging on the successful completion of these deliverables on-time.
Invoices are raised based on the completion of these deliverables which will then have to be checked and paid out. In the procure-to-pay process, manual and spreadsheet- based processes are deployed for identification of products and services, the creation of purchase orders, verification of goods/services, receiving invoices, performing a 3-way match and making the payments.
Then there are carefully choreographed processes of drilling and pipelining which leave very little room for errors as any breakdown can result in significant loss of time and money. Companies sometimes burn significant idle labor charges while delays happen, which run into millions of dollars over the lifetime of a long-duration project.
Extreme automation into the mix
Digital oilfields, digital rigs, smart refineries, and intelligent pipeline networks managed at remote control centers are being built to simulate, replicate and monitor operational parameters and completion of performance targets in real time.
Capital performance dashboards, enabled through smart analytics and machine learning algorithms, can highlight project performance against planned and forecasted data and highlight specific areas of risks and improvements.
Automated drilling solutions and automated pipeline robots or digital “roughnecks” are being designed to bring down the level of manual involvement and improve safety in operations.
A paperless digital system, enabled on handheld devices and linked to all the relevant software platforms, allows for information handover, commissioning and startup related activities to be tracked and managed more effectively.
Robotic Process Automation (RPA) is increasingly being used to automate reconciliation of the completion of deliverables such as status tracking, alerts, monitoring and invoicing.
Measurement of pipeline flow and pressure can be significantly automated using sensors, LiDARs, 5G or Near Field Wireless networks. Analysis of past performance of the engineering, production and construction (EPC) contractors in terms of their progress vs. plan, their change requests, their design capabilities or the effectiveness of the procurement process can all be done with the help of big data analytics. Some of the information exchanged and handed over can potentially be completely transformed using Blockchain technologies. By looking at past data, self-learning health and safety incident models can be used to predict possible risks with a high level of accuracy and certainty.
Geo-fencing coupled with video and image analytics captured by drones can improve remote asset monitoring, site safety and security. A live, high-quality 3D model, linked to other systems such as completion or maintenance, and accessed on touchscreens with progress forecast visualizations (4D), will dramatically improve onshore work preparation– reducing survey times, increasing collaboration and allowing quicker interventions.
Taking full advantages of Extreme Automation, oil and gas companies can plan better and commission faster – thereby attaining massive improvement in capital efficiency.
Fuelling operational efficiency
Identifying opportunities for operational improvement has always been high on the agenda for oil executives ranging from refinery supervisors to plant operations managers to COOs. The traditional approach has always been to attempt a reduction in workforce, reduction of downtime, or by robot izing the sites.
A major hurdle in achieving operational efficiency is that Information Technology and Operations Technology are looked at in silos– which inhibits a high degree of collaboration and integration. If this IT/OT integration
is made a priority, the loop between operational planning, plant/ site observations, and enterprise solutions can be effectively closed. The true potential of IT/OT integration can only be realized when say, a pump self-diagnoses and detects issues with the rotors, uses predictive analytics to identify the need for replacement in x number of days, orders the part in the sourcing system, tracks shipping, detects supply disruptions, publishes the component design to 3D-print the parts, and then instructs a robot to put together the parts into an assembly.
Extreme automation approaches present us with better and more effective ways of achieving higher operational efficiency and plant reliability. An intelligent plant operations management solution can integrate operational data from innumerable sources, including those generated by equipment, to deliver notifications and predictive analytics reports to site engineers so they can identify performance issues even before they become significant enough to affect operations.
Extreme automation has a potential to radically transform operations
An Operations Workbench can enable the workforce to access all information such as procedures and operating manuals on a handheld mobile device that synchronizes seamlessly with the enterprise knowledge graph. Machine learning algorithms, aided by Natural Language Processing (NLP) and Optical Character Recognition (OCR), are increasingly being used to interpret unstructured hand-written or voice-recorded operational comments and take corrective actions. Predictive analytics will drive condition-based maintenance rather than the timeline the original equipment manufacturers (OEM) prescribes, thus saving dollars and improving safety.
Availability of time-series sensor data and the automation of processes and equipment has enabled remote operations, so far seen primarily in automobile and mining sectors. Unmanned, untethered autonomous surface vehicles (ASV) and autonomous underwater vehicles (AUV) enable real-time pipeline integrity and inspection. Intelligent materials management and 3D printing have changed how parts are sourced, procured and installed. The oil and gas industry has been going through a great “crew change” phenomenon wherein baby-boomers are retiring and Gen Xers and Millennials are joining the workforce, resulting in the loss of documented enterprise knowledge (acquired largely through experience), an increase in the risk appetite and restlessness, and the loss of the culture of “employee-for-life.”This exemplifies the need to impart training faster and better. The on-boarding process is being accelerated by the use of augmented/virtual reality courses which provide intense immersive experiences (like the airline pilot training) and prepares the new generation to perform the work in a controlled, safe environment– ready to face any potential eventualities.
Oiling the wheels of supply chain efficiency
Supply chain networks play a significant role in keeping the wheels moving in the oil and gas value chain. While an oilfield services company might want to improve flexibility in the movement of their equipment, replacement parts and other material supplies, a pipeline operator might need predictability of supply to optimize the available capacity, while a trading operator would need to have a holistic view of inventory across tanks and terminals, or a refiner would need to manage the change in product mix, in real time, related to the changing nature of demand and regulations.
Supply chain inefficiencies can be addressed in a bi-modal manner through a macro view of the whole network and a micro view of each movement and inventory to ensure that the whole network is efficient. Some of the ways in which these can be achieved would be:
- Capability to predict customer and product-mix demand beyond looking at seasonal trends and historical trends
- Identifying the need for capital investments early- on by analyzing the change in the spend patterns, sourcing behavior, capacity requirements, changes in drilling technologies, etc.
- Modeling inventory level fluctuations across the network through real-time monitoring of tank levels (against safety/overstock situations) and loading rack configurations at refineries and terminals
Many oil and gas supermajors are setting up control towers with real-time material, people and hydrocarbon flow information – feeding into them to proactively manage disruptions. Advanced neural network-based machine learning models are used to model demand forecasts, especially in the volatile spot markets, and devise a strategy to re-route cargo in lucrative markets providing arbitrage opportunities. There is an increased collaboration between all parties in the supply chain network using Blockchain-aided smart contracts. At the micro level, intelligent pigs are used to monitor pipeline batches and change in the product quality while it is being moved in the pipeline. Some companies are already thinking about dynamic blending happening in pipes as against the traditional in- tank approach.
Land-based geo-location devices, aided by 5G communication technology, can help in pinpointing the location of barges, trucks, or rails to ensure that parcels are located and delivered on time, thereby minimizing demurrage charges. Terminals systems are getting modernized to ensure that mobility technologies and IoT sensors are used to record tank stocks. RFID tagging and other track-and- trace technologies can be used to monitor the movement of drilling equipment, downhole lubricants, and MRO supplies. Concepts like Amazon Go are being thought of to build card-less/cash-less payments made on forecourt and in-store.
Adopting extreme automation can undoubtedly make the oil and gas supply networks more efficient, thereby smoothing the overall cost-to-serve curves, leading to better margins in this price-sensitive environment.
Transforming headwinds into a full gale
Oil and gas will remain a major component of the global energy mix and the recent strides the industry has made in opening up to digital technologies heralds a favorable turn in the tides.
With the great crew change in progress, the future seems to belong to the digital world where humans, equipped by the right data and aided by a digital co-worker, will only take critical decisions, leaving the rest of the process to be managed by various components of Extreme Automation landscape. To take innovation to the next level in oil and gas, it is critical that process barriers between operating business functions are brought down, as looking for efficiency improvement in silos can only get limited results.
Price volatility is here to stay and the only way oil and gas companies can maintain margins and dividend payouts is by adopting a manufacturing mindset, and embracing digital technologies and extreme automation.