Improving sustainability throughout the automotive product lifecycle
Sustainability must be designed into the product lifecycle and cannot be an afterthought for automotive companies.
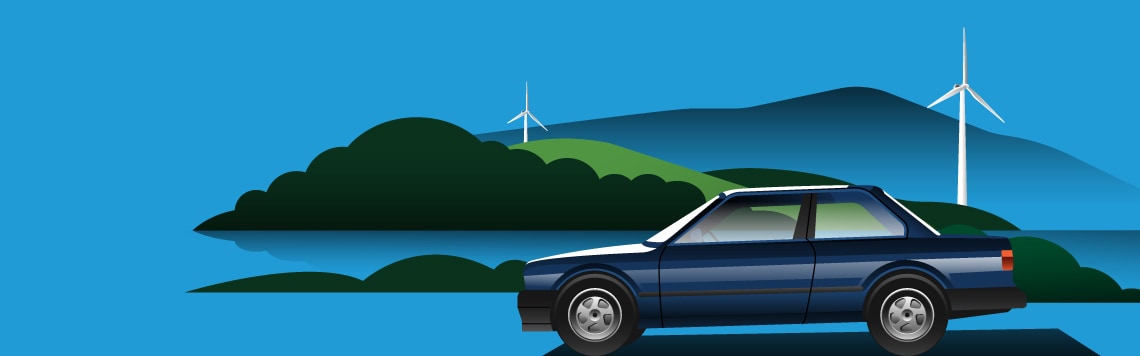
Climate change is possibly the biggest threat faced by modern human beings. When the concentration of greenhouse gases – carbon dioxide, methane, nitrous oxide – increases in the atmosphere, it produces a warming effect that is devastating to the environment. From scorching heat waves to torrential rains, from raging wildfires to unseasonal deep freeze, we suffered all this and more in just a single year, 2021.
Tragically, human activity is almost solely responsible for the increase in greenhouse gases in the past hundred years. And activities, which involve burning fossil fuels, are more responsible than others. For example, 29 percent of the 6.6 billion tons of U.S. emissions in 2019 was caused by the transportation sector, followed by electricity (25 percent) and industry (23 percent).
Passenger cars contributed the most (41 percent) to transportation emissions in the U.S in 2019. The automobile industry emits greenhouse gases in all three categories, namely scope 1, 2 and 3, defined by the Greenhouse Gas Protocol, a popular framework used for emission reporting and management. Since Scope 1 and 2 emissions are directly linked to the operations of automotive manufacturers, the companies have fairly good visibility and control over them. On the other hand, scope 3 emissions, which originate in the supply chain and logistics network, are harder to ascertain and almost impossible to control; but since they constitute the bulk of automotive emissions – about 80 percent on average and a whopping 98.1 percent at Toyota Industries – there is no way that vehicle manufacturers can look the other way.
A major sustainability initiative of the automobile industry is the electrification of cars. Electric vehicles (EVs) eliminate the (scope 3) tail pipe emission seen in internal combustion engine-driven vehicles. But tail pipe emission is only a small part of the problem. To make a real dent, automotive manufacturers need to improve sustainability at every stage of the product lifecycle.
Sustainable by design
The automotive product lifecycle starts with design, which has a strong bearing on the total quantity of emissions during the subsequent stages. Today, the definition of a well-designed car includes sustainability metrics, such as fuel efficiency, circularity of materials, and low waste. Hence vehicle manufacturers are experimenting with design ideas, such as light-weighting – reducing a vehicle’s mass to cut fuel consumption during its lifetime and scrap waste, thereafter. General Motors uses artificial intelligence for generative design, creating hundreds of design options for an automobile part and selecting the best out of them.
Car makers are also taking new product development out of energy-intensive workstations, and on to the public cloud to shrink their carbon footprint. Our recent research revealed that amid accelerated digital transformation in the wake of the pandemic, new product development became the second most important reason for cloud adoption among discrete manufacturers. Toyota, for example, implemented virtual desktop infrastructure on cloud so engineers could collaborate from remote locations; this also saved costs by reducing the number of workstations, and improving computing utilization.
Make better use of manufacturing resources
As it happens, the pandemic forced one more sustainable practice in automotive manufacturing, which is “make to order”. With chip shortages and other supply chain bottlenecks crippling production, automobile companies could no longer manufacture several months sales worth of units and stock them in dealerships. To tide over the problem, they switched to a “make to order” business model, producing cars only against orders. This is not unlike the just-in-time model long favored by Japanese car makers.
Making to order is more sustainable than making to stock because it creates much less waste – not only of the materials and energy used directly to produce the car, but also of the resources involved in transporting and warehousing it.
Here are some ways in which the industry can become resource-efficient: Ford is recycling used water to meet its target of zero clean water usage. Tesla plans to use solar energy in its Gigafactory to eventually reach net zero in energy consumption. Manufacturers can also become more responsible by employing digital technologies, such as the Internet of Things, to track resource usage in granular detail. General Motors is scaling back nice-to-have, but optional, features – for example seat warming and cooling – in a move towards frugal, sustainable engineering.
Source ethically and responsibly
A single vehicle has about 30,000 parts on average, procured through a complex supply chain. For example, Ford has 1,200 tier-1 suppliers providing parts composed of about 1,000 materials. Automotive manufacturers should not only monitor GHG emissions across their supply chain (scope 3) but also ensure vendors comply with all legal and ethical obligations.
One of the items on the sustainability watchlist is conflict minerals. In 2021, the European Union enforced the Conflict Minerals Regulation requiring users of tin, tantalum, tungsten and gold to ensure they sourced from responsible suppliers and did not help to fund armed conflict or other illegal activities. This means automobile companies must know the provenance of the conflict minerals used in their products, and also the processes they underwent before ending up in their supplies. The problem is that like it is with scope 3 emissions, vehicle manufacturers have had little to no visibility into raw material supplies. But now blockchain – and others like it – is bringing traceability to the supply chain, enabling manufacturers to track everything from provenance to processing to physical location of each and every material that is sourced, on a secure and immutable distributed ledger.
Suppliers, who are mostly small enterprises, usually do not have the resources or knowledge to practice sustainability. It is incumbent on automobile manufacturers to support and mentor them in this direction. Jaguar Land Rover has set a good example with its online collaboration platform for suppliers, which has helped shorten the cycle time for certain product development tasks by 40 percent.
Be sustainable on-road and beyond
Sustainability in the delivery stage of the automotive lifecycle can be improved by minimizing emissions during transportation. Car makers are piloting green, electric trucks for the delivery of finished vehicles. Skoda, for example, has piloted battery-driven trucks for its internal logistics.
Vehicles on the road are bound by emission norms that limit their impact on the environment. But with automobiles turning electric with onboard electronics, there is a lot more that manufacturers can do to improve sustainability during performance. Connected cars send enormous data over the IoT, offering insights into their health, usage, on-road behavior, and more. Manufacturers can remotely monitor that information – without violating privacy and other data regulations – and send timely alerts should they see a drop in sustainability parameters. This also helps to lower repair costs and extend the life of the vehicle.
The United States alone generates several billion tons of industrial waste each year. Cost apart, this exacts a huge toll on the environment by dumping into landfills. “Zero waste” is therefore a huge priority for the manufacturing industry that it can achieve by following circular principles – design out waste and pollution, keep products and materials in use, and regenerate natural systems.
So, instead of scrapping a car at the end of its useful life, manufacturers should salvage its parts and materials for reuse. With the cost of materials, and even of used cars, climbing in markets like the U.S. there is a strong economic rationale for keeping materials in circulation for as long as possible. This is why the Renault Group has made it a priority to gradually replace natural raw materials with secondary materials made from recycling.
In short
Sustainability is one of the biggest priorities of the automotive industry today. Thus far, sustainability has seeped into only some parts of the business – for example, vehicle design and manufacturing. To be truly sustainable, car manufacturers must replace piecemeal action with a holistic sustainability strategy covering the entire product lifecycle, from conceptualization and design, to sourcing and production, delivery, after-sales, and even end-of-life. While this is a huge challenge, automobile companies have access to a range of digital technologies that can support them at every stage.